Week 7.2: Performance Measurement and Improvement
Six Sigma and Total Quality Management (TQM). Six Sigma is a data-driven methodology that aims to improve process quality by reducing variability and defects. By monitoring key metrics and implementing strategies for continuous improvement, companies can identify areas of weakness and develop targeted solutions to improve efficiency, reduce costs, and enhance customer satisfaction.
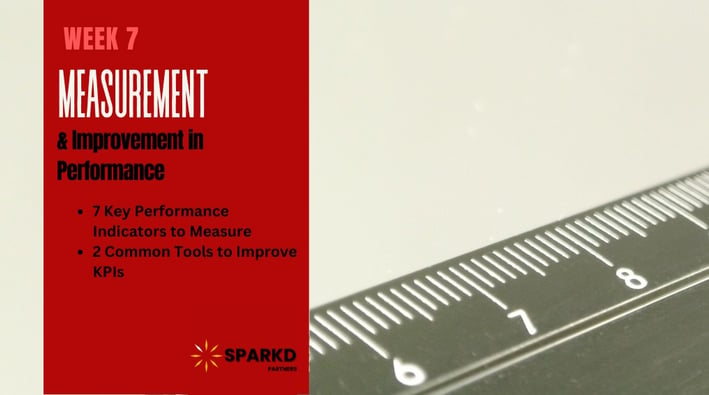
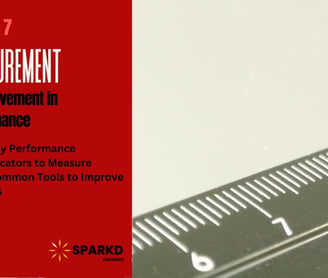
Measuring Supply Chain Performance (Part 2)
To improve performance and achieve business success, companies can use a range of strategies for continuous improvement in the supply chain. Here are 2 easy strategies:
Six Sigma
A data-driven methodology that aims to improve the quality of processes by reducing variability and defects. You can implement the Six Sigma by:
Define: Define the problem and the goals of the project. This includes identifying the process to be improved and the customer requirements.
Measure: Measure the current performance of the process. Collect data on the process and analyze it to determine your baseline performance.
Analyze: In this step, the data is analyzed to identify the root cause of the problem. This may involve using statistical tools to identify patterns and trends in the data.
Improve: Once the root cause is identified, develop and implement solutions to address the problem. This may involve redesigning the process or making changes to the existing process.
Control: The final step is to control and monitor the improved process to ensure that it remains stable and continues to meet customer requirements. This involves establishing metrics to measure the process performance and implementing controls to prevent defects from occurring.
Total quality management (TQM)
The second most commonly used management approach that focuses on continuously improving the quality of products and services is TQM. You can implement TQM by:
Customer Focus: Understand the needs and expectations of your customers. This includes identifying the customer requirements, expectations, and feedback.
Continuous Improvement: Next, continually improve the quality of products and services. Identifying any areas of improvement, analyzing problem root causes, and develop solutions for them.
Employee Involvement: TQM recognizes the importance of involving employees in the improvement process. This includes training employees in quality management principles and encouraging them to participate in problem-solving and decision-making.
Process Management: Management of processes to ensure consistent quality is one of the key points of TQM. Define the processes, establishing performance metrics, and monitor its performance.
Leadership: TQM requires strong leadership commitment to quality. Leaders must set the example, establish a quality-focused culture, and provide the necessary resources for improvement initiatives.
Strategic Planning: Align quality goals with the organization's mission and vision. Set quality objectives, develop a standard and allocate resources to achieve your objectives.
Unlike Six Sigma, TQM is a customer-focused, data-driven management approach that emphasizes continuous improvement and employee involvement to achieve high levels of quality in products and services.
Six Sigma is a data-driven methodology that focuses on identifying and eliminating defects and reducing variability in a specific process to improve quality and efficiency.
By implementing these strategies and monitoring key performance indicators, companies can continuously improve their supply chain operations and achieve greater success.
Bear in mind, performance measurement and improvement are crucial components of success in supply chain management. With measurement of key metrics and timely implementation of strategies for continuous improvement, companies can identify areas of weakness and develop targeted solutions to improve efficiency, reduce costs, and enhance customer satisfaction.
Strategies for continuous improvement in supply chain
Prefer to read it all in one go as a PDF? Get the 7-Step Supply Chain Crash Course here.
We offer a range of services and resources to help companies achieve greater success in their supply chain operations.
Let's partner up and create a more resilient supply chain for your company. Get in touch now.